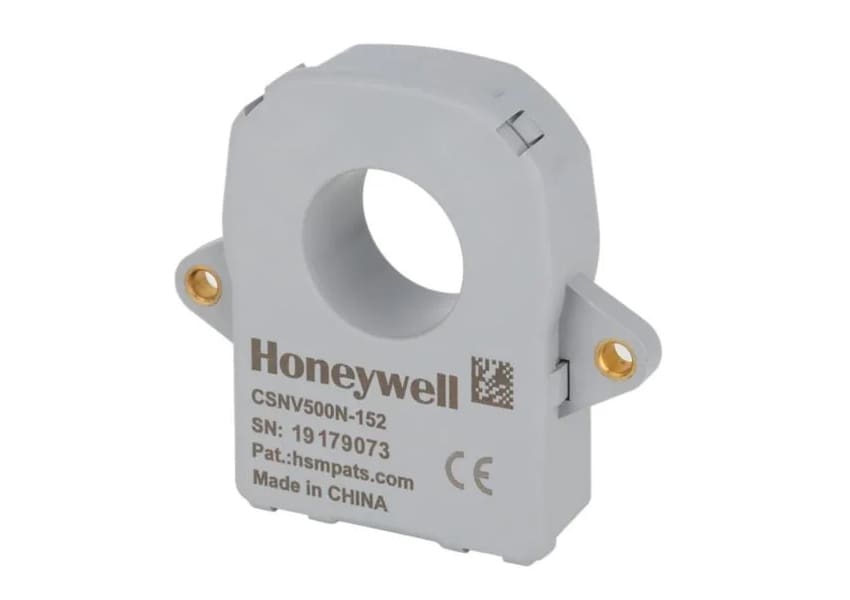
Sponsored by TTI.
Whether or not for the BMS or motor management, listed below are the important thing specs to grasp when
sourcing these crucial EV parts.
Electrical autos proceed to develop in recognition and market share, and electrical present is the gasoline of the long run. Present sensors are a crucial part of at this time’s EVs, serving two main functions in line with Ajibola Fowowe, world providing supervisor at Honeywell.
“The battery administration system (BMS) makes use of present sensors, together with different sensors such because the voltage and temperature sensors, to observe the state of cost and general well being of the battery pack. The opposite use for present sensors is in motor management, the place it’s relied on to shortly detect and isolate a fault within the electrical drive,” stated Fowowe.
Whatever the use case, there are a number of issues EV engineers should perceive when choosing among the many many obtainable present sensors. Right here’s what it’s essential know.
Sorts of EV present sensors
There are several types of present sensors that every have benefits and drawbacks for EV functions.
Closed loop present sensors
Closed loop present sensors have a suggestions system for improved measurement accuracy. A magnetic core concentrates the magnetic discipline generated by the stream of present and gives a proportional voltage to the quantity of present detected within the core. This permits the sensor to generate a exact present measurement. Due to their excessive accuracy and stability, closed loop sensors are effectively fitted to use within the BMS.
The Honeywell CSNV 500 (pictured above) is a closed loop present sensor rated for a main present measurement vary of ±500 amps of direct present. The CSNV 500 includes a proprietary Honeywell temperature compensation algorithm with digital CAN output, to supply excessive accuracy readings inside ±0.5% error over the temperature vary of -40⁰ to 85⁰ C for strong system efficiency and reliability.
Open loop present sensors
Open loop present sensors function on the precept of magnetic induction. They include a main winding, via which the present travels, and a secondary winding that measures the induced voltage. Open loop sensors require much less extra electronics and processing in comparison with closed loop sensors, leading to sooner response occasions. Nonetheless, they require extra calibration as a result of they’re extra susceptible to variations in warmth and magnetic discipline. This implies they’re additionally much less correct — reaching roughly 2% error of the first readings.
The quick response time of open loop present sensors makes them preferrred for motor management capabilities. Motor management functions don’t require the identical stage of precision because the BMS, so the lack of accuracy in comparison with a closed loop or flux gate sensor isn’t crucial.
The Honeywell CSHV line of open loop sensors have a spread of 100 amps to 1,500 amps, and their response occasions are as quick as six microseconds. They’re utilized in fault isolation and fault detection, in addition to controlling motor velocity. They will also be utilized in battery administration techniques that don’t require very excessive accuracy, equivalent to in hybrid electrical autos. These sensors use AEC-Q100 certified built-in circuits to satisfy prime quality and reliability necessities.
The Honeywell CSHV sequence open loop sensor
Honeywell’s CSNV 1500 has each closed loop and open loop performance. This permits the sensor to satisfy an accuracy requirement of 1%, and is designed for functions that require excessive accuracy. The CSNV 1500 is used for related EV functions because the CSNV 500, in addition to stationary vitality storage techniques and industrial operations.
Flux gate present sensors
Flux gate present sensors measure adjustments within the magnetic flux of a present because it passes via a magnetic loop, from which it will possibly derive present measurements. The Honeywell CSNV 700 is designed for functions that fall between 500 A and 1,000 A necessities. It has a greater zero-offset and better sensing vary than 500 amps sensors—nevertheless it additionally has larger energy consumption than a closed loop sensor. The CSNV 700 has related accuracy ranking because the CSNV 500, at 0.5%, and it additionally makes use of AEC-Q100 certified built-in circuits.
As with closed loop sensors, the flux gate sensor is greatest utilized in BMS settings that require excessive accuracy. When utilizing flux gate sensors, nevertheless, engineers have to be aware of their larger energy necessities, which might devour extra battery vitality.
Honeywell’s CSSV 1500 is a mix open loop and flux gate sensor. It was designed to satisfy Automotive Security Integrity Stage C (ASIL-C) necessities for safety-critical functions the place prospects need the next stage of reliability and efficiency. Whereas many 1500 A sensors devour extra energy, the mixture of open loop and flux gate applied sciences makes use of much less energy whereas nonetheless assembly the accuracy and useful security necessities. It meets Automotive Security Integrity Stage C (ASIL C) necessities for security crucial functions. This requirement is typical of battery electrical autos (BEV).
Shunt present sensors
A shunt present sensor measures the voltage drop throughout a way resistor positioned within the conduction path between an influence supply and a load. It’s an inline present sensor linked on to the busbar; closed loop, open loop and flux gate sensors are non-contact sensors that don’t have that direct connection.
One of many advantages of a shunt sensor is that it will possibly present an instantaneous measurement of present. Nonetheless, it generates extra warmth and contributes to energy loss within the circuit. This creates parasitic vitality waste. Fowowe says that developments in shunt expertise is growing its attractiveness in excessive voltage techniques and Honeywell is actively researching extra worth that may be derived from the applying of shunt expertise such because the potential mixture of present and voltage measurements into one sensor to cut back the general value of the BMS.
Different key issues for EV present sensors
Along with contemplating which sensor to make use of by which utility, engineers will even have to consider different variables. Because the sensor must work correctly in a magnetized atmosphere, its capability to deal with magnetic interference is necessary. For BMS functions that depend on a excessive stage of accuracy, engineers might want to contemplate the sensor’s zero-offset, which is the quantity of deviation in output or studying from the bottom finish of the measurement vary.
Ease of integration can be necessary to think about. EVs can use both controller space community (CAN bus) commonplace or analog outputs. CAN communication is extra widespread within the BMS. CAN bus communication velocity is restricted by the CAN protocol to 10 milliseconds, which is appropriate for the BMS. For extra rapid measurements, motor management capabilities use analog outputs, which might reply in microseconds.
One other issue to be aware of is the EV’s driving atmosphere. EVs want to have the ability to perform correctly in any situations, from a warmth wave in Arizona to a snowstorm in New York. Subsequently, the sensor’s working temperature vary must be factored in. In line with Fowowe, Honeywell’s sensors are constructed to keep up efficiency in temperatures starting from -40 to 85 levels Celsius; the sensors function a Honeywell patented multi-point temperature compensation algorithm to make sure the sensors can ship very excessive accuracy and efficiency underneath any driving situation.
To study extra about present sensors for EVs, go to Honeywell at TTI.